Skupina ČD / Dynamický zkušební stav VUZ aneb tady je fyzika doma
Dynamický zkušební stav VUZ aneb tady je fyzika doma
2.11.2020 – autor: JOSEF HOLEK
Dynamický zkušební stav (DZS) Výzkumného Ústavu Železničního (VUZ) může leckomu připadat jako ocelové město protkané kabely, hydraulickými hadicemi, počítači a díly pro železniční kolejová vozidla všeho druhu. Zdánlivý nepořádek ale má svůj přesný řád. Jde přece jen o špičkové pracoviště, kde působí specialisté milující fyziku a kde pracují přístroje, které trhají a zapalují ocel. Měli jsme jedinečnou možnost podívat se na dvě zkoušky.
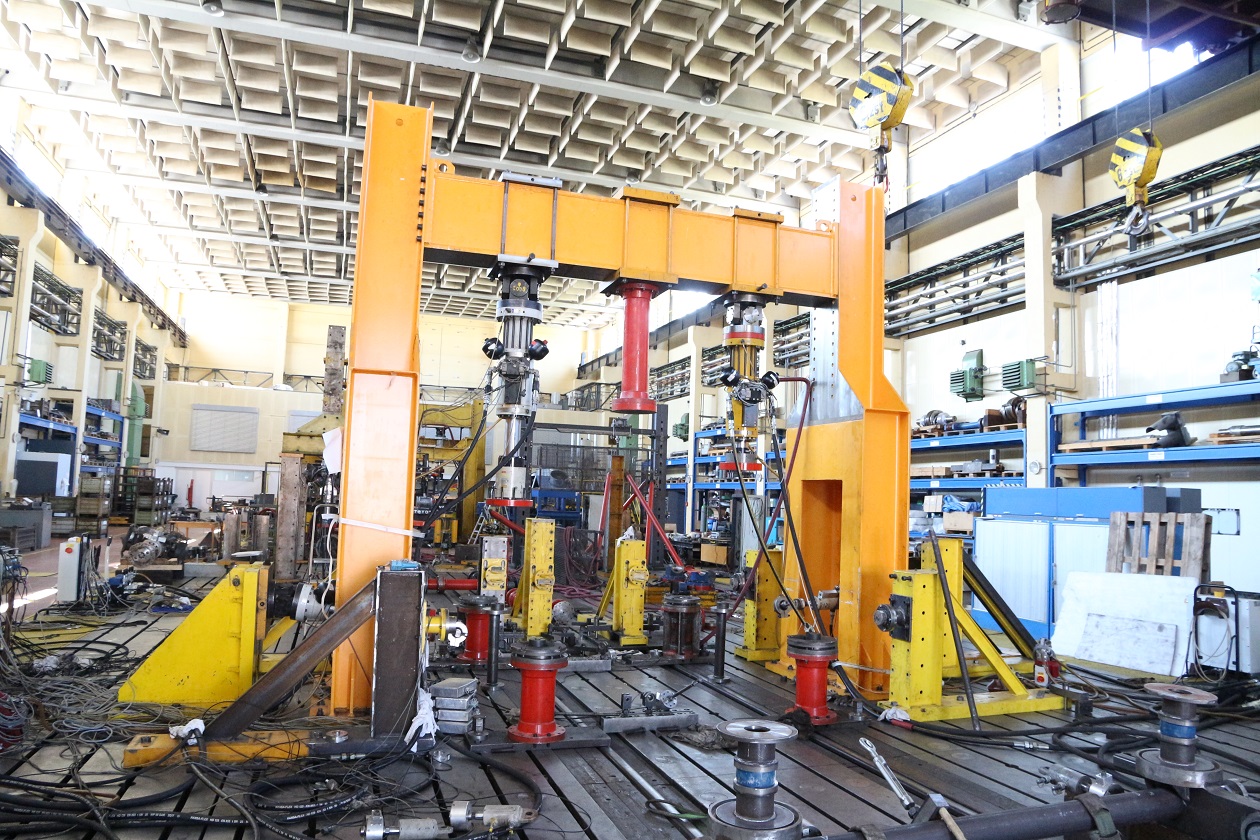
Zkraje se musím přiznat. Na základní škole ani gymnáziu mi fyzika moc neimponovala a obor vystudované vysoké školy je jí vzdálený na hony. Ale techniku mám rád, a když se něco hýbe, zajímá mě princip fungování. Když jsem dostal možnost podívat se na dvě zkoušky na DZS, jenž je součástí Zkušebního centra VUZ Velim, neváhal jsem ani vteřinu a rád ji využil.
U dveří obří žluté haly, která centru dominuje, mě vítá vedoucí DZS Jiří Soukup. Obléká mě do reflexní vesty, nasazuje povinnou helmu a seznamuje s programem. Nejprve se podíváme na zkoušky rámu podvozku pro elektrickou jednotku a poté si nechám ukázat, jak ve VUZ zapalují ocelová kola pro všechna ŽKV. Ano, čtete správně. Zapalují ocel. Jistě, jde o zkoušku, při které se simuluje sjezd z klesání těžkého vlaku rychlostí 60 km/h. Ale nepředbíhejme.
Realita je jinde
U velkého šedivého rámu budeme nejdříve kontrolovat svary. „Jde o kritickou část rámu podvozků, která spojuje jednotlivé části,“ vysvětluje Jiří Soukup. Předpokládá se, že když je rám konstrukčně správně navržený, kritická místa při únavových a statických zkouškách neprasknou. Jenže díl nemusí být dokonale svařený ani dokonale navržený. Svary tedy pracovníci nastříkají speciální bílou podkladovou barvou tak, aby byl zvýrazněn kontrast mezi svarem a dílem. Do díla se poté pustí elektromagnet, velká dvoupólová vidlička. „Jeho pomocí vytvářím magnetické pole mezi dvěma póly, a pokud je ve svaru trhlina, pomocí barevného magnetického prášku, který v sobě obsahuje malé kovové částečky zatékající do všech skulin, se objeví indikace trhliny,“ konstatuje. Trhlina se projeví jako černý proužek. Výrobce má štěstí, nenašli jsme nic.
Příprava na tuto zkoušku trvá celý den. Dnes už jsou konstrukce svařované na základě výsledků počítačových simulací. Ovšem pokud je díl vyroben, může se realita trochu lišit. Pořád můžete veškeré komponenty špatně svařit. Po zkoušce následuje sepsání protokolu o tom, čím a jak jsme zkoušeli a za jakých podmínek.
Pod dráty
Mezi tím kolegové pana Soukupa polepili rám miniaturními senzory, za kterými se táhnou pavučiny drátků. A vězte, specialisté z VUZ se v té spleti vyznají. Měřit budeme povrchové napětí na rámu, při zatížení. Laicky řečeno, změříme deformaci dílů v jednotlivých bodech. Rám už před zkouškou projde u výrobce simulačním výpočtem a z výsledků simulací dokážou specialisté VUZ určit, kde jsou kritická místa. Místa, která se mohou deformovat (a poškodit se) a na ně speciálním lepidlem přilepit tenzometr. Když se deformuje kov, deformuje se i tenzometr. Jednoduché.
Tenzometr není ničím jiným než drobounkou mřížkou s drátkem, který mechanické napětí snímá. Abychom mohli zkoušce věřit, musíme díl osadit více tenzometry a zapojit je do Winstonova můstku. Při deformaci se mění elektrický odpor tenzometru, na základě čehož je získána velikost mechanického napětí v určitém místě. Měřené elektrické napětí je totiž přímo úměrné mechanickému napětí, které potřebujeme zjistit. Kolik musí díl vydržet? Deset milionů cyklů. Osm bez jakékoliv trhliny. V podstatě jde o ekvivalent třicetileté životnosti. A dál? Protokol.
Následuje přesun k sestavě zkoušky. Proč ale nemůžeme rám vysokozdvižným vozíkem položit na nosnou konstrukci, zapnout a jít? Tady příprava na zkoušku trvá i několik týdnů. Pro každý rám podvozku se musí navrhnout speciální instalační přípravky. Představte si je jako různé svařence, čepy, nebo kloubová zařízení, pomocí nichž se k rámu připojují hydraulické válce. „Vše pevně sešroubujeme, vložíme do zkušebního stavu. Zkouška se musí přiblížit tomu, jak je rám zatěžovaný v reálu,“ konstatuje vedoucí.
Čtyři válce na jeden rám
Teprve když je rám pevně uchycen ve všech bodech, v počítačovém programu nastavíme předem definované signály pro hydraulické válce, které se postarají o samotnou zkoušku. O přesnost se ve válcích starají senzory, které vnímají zpětnou vazbu. Počítač si pak řídí, jak má rám zatížit. Následuje rychlé stlačování válci. Jednotlivé hydraulické válce vyvozují sinusový signál, podle nastavené frekvence. Jde například o 4 Hz, což značí čtyři stlačení za vteřinu. Každý válec kmitá mezi předem nastavenými silami, které závisí na druhu rámu podvozku, tak aby se zatížení rámu co nejvíce přiblížilo skutečnému provozu. Dva válce jsou jako na pružinách, další dva po bocích simulující příčné zatížení. Všechny kmitají spolu a simulují průjezd rámu podvozku při plném zatížení, při plné rychlosti, po koleji v obloucích.
Ročně VUZ zvládne detailně proměřit čtyři až pět rámů. Zkouška trvá obvykle dva až tři měsíce. Když je testování složitější, třeba při nasazení 16 válců, pak i půl roku. „Měsíc vše připravujeme, další půldruhý měsíc běží stav nonstop. Pokud něco praskne na rámu podvozku, zkouška končí.“ V případě, že specialisté najdou defekt po osmi milionech cyklů, informují zákazníka a sepíší protokol. Při kontrole po deseti milionech cyklů už být trhliny mohou. Pokud trhlina vznikne před dosažením 8 mil. cyklů, zákazníkovi nezbývá, než provést konstrukční úpravy a dát si testovací kolečko znovu s tím, že pokud se dílčí testy podaří napoprvé, už se nemusí opakovat.
Po několikaměsíčním snažení, kdy se konstrukce namáhají dynamickými i statickými silami, musí snést neskutečné zatěžování, jde rám ven. Vypadá v podstatě pořád stejně. A že by měl vypadat jako zmačkaná plechovka? Vůbec. Podle prvního a úspěšně otestovaného mustru se pak vyrábí všechny ostatní kusy.
Když šlehají plameny
Ve zkušebně pro termomechanické zkoušky kol specialisté VUZ simulují sjezd vlaku z prudkého kopce při kontinuálním brždění a za určité rychlosti. Zkouška je koncipována tak, že se kolo vloží pomocí závěsného navijáku do speciálního brzdového modulu, ložiska se uchytí do „domků“, z každé strany namontují špalíkové brzdy, připojí k hřídeli hnacího motoru, a jede se. Systém je řízený počítačem a kolo roztáčí postupně na rychlost 60 km/h. O měření deformace věnce kola se starají lasery. Uprostřed kola je ještě indukční snímač, který snímá vzdálenost na prostředku. Lasery měří, jak se kolo při totální deceleraci deformuje. Cyklus trvá 45 minut a na kolo je aplikován brzdný výkon až 50 kW. To je plně naložený nákladní vůz. Proti tomu motor stále točí šedesátkou. Po dvaceti minutách už začíná kolo třením svítit, má teplotu až 400 °C. Po pětatřiceti až 450 °C, špalky hoří a pomalu začíná hořet i ocel. Měříme. Kraje se ohýbají do boku, jako by se chtěly zavřít. Střed drží, ale mění se rozkolí a vůz by nyní vykolejil. Nás však zajímá, o kolik se kolo zdeformovalo. Povoleny jsou plus tři milimetry dovnitř kolejí a 1,5 mm směrem ven, na okolek při brždění. Více ne. Při chladnutí se materiál deformačně vrací, ale ne do původního stavu. Opět chceme vědět, do jakého stavu se pak kolo při vychladnutí dostane. Zkouška se vším všudy, včetně chladnutí a dalších úkonů, trvá pět dní pro jeden kus kola. A často se stává, že kola neprojdou. Prasknou anebo se zdeformují nad míru. Ročně zmákneme dvacet až třicet kusů. Zkouškou musí projít vždy ojeté i neojeté pro každý typ. „Při provozu je standardní praxe, že jsou kola přesoustružována, a tedy musí mít vyhovující termomechanické vlastnosti jak nové, tak mezně opotřebované kolo,“ říká vedoucí DZS Jiří Soukup. Celý systém musí být chlazen vzduchem, který proudí rychlostí 30 km/h.
Další články této rubriky
Pražské datové centrum se výrazně rozšířilo
8.3.2025 - Dceřiná společnost Českých drah ČD - Telematika v lednu dokončila a zkolaudovala už čtvrtý technologický sál svého hlavního datového centra v Praze 9. Díky investici ve výši několika desítek milionů korun se po sedmi letech od… »
Pokud budeme důsledně postupovat podle nařízení č. 402/2013, pak doba psaní předpisů „krví“ skončila
1.1.2025 - Železnice denně přepraví miliony cestujících i tuny zboží. S vysokými nároky na spolehlivost, bezpečnost a efektivitu je nezbytné pečlivě sledovat a řídit rizika, která by mohla ohrozit plynulost provozu nebo bezpečnost… »
Zajímavosti z provozu ČD Cargo na Liberecku
18.11.2024 - Letošní rok byl na Liberecku opět ve znamení rozsáhlé výlukové činnosti. V prvním pololetí byl rekonstruován podjezd pod libereckým nádražím s výrazným dopadem na nákladní dopravu. Ta mohla využívat pouze část staničních… »